Generative design of chassis parts
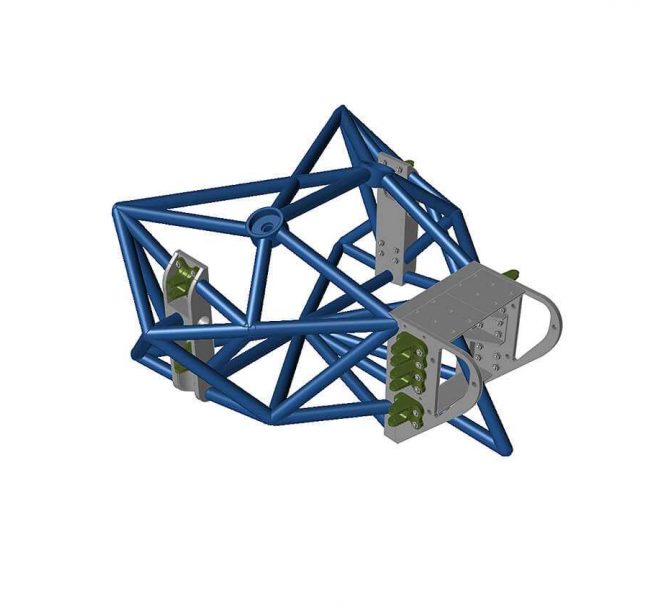
Design lightweight components to improve performance of fully electric race car
In recent years, generative design is increasingly used in a multitude of industries to help the conceptualization of more efficient, lightweight and sustainable products. A broad discussion is going on, in the engineering community, about the exact definition of generative design and its comparison to other technologies. A good read is available by engineering.com.
In this project Optiphore and InMotion have collaborated on efficiently designing a number of brackets connecting a tubular frame at the rear end of the vehicle with the suspension links. Among other things efficient design implies lightweight components. This is important for the performance and range of every Battery Electric Vehicle (BEV) and even more so in the case of a race car. Another interesting aspect for InMotion was to go beyond costly ‘trial & error’ design approach and fully exploit the benefits of up to date, efficient methods like generative design.
InMotion provided all relevant inputs, such as existing CAD design, material information and an envelope of all load cases. Moreover, additional restrictions were taken into account, such as the fact that additive manufacturing was not considered as an option and hence the designed components would be manufactured using traditional machining techniques.
Utilizing these inputs, we defined a proper design space, in close collaboration with the engineering team of InMotion. Subsequently, topology optimization studies were executed using Altair’s Inspire. After the necessary iterations, results were interpreted into a production ready CAD model and the new optimized parts were validated by structural analysis.
The optimized structure is about 20% lighter than its original design, while maintaining the desired structural performance. This project is one of many examples of how Optiphore offers ‘end-to-end’ development. In this specific case, not only did we use optimization techniques to improve the design but we also interpreted the optimization results in a fully detailed, ready to manufacture CAD model.
“The results are something the entire team was very happy hearing, a 6 kg loss in weight is a big step for the frame.”
Teun van den Einden – Structural Engineer
About InMotion
InMotion is a students’ team based in Eindhoven. InMotion’s mission is to make charging as fast and convenient as refueling of petrol cars. The team will showcase the potential of electric refueling by joining in the Garage 56 class during the 24 Hours of Le Mans with a fully electric endurance race car in 2023.
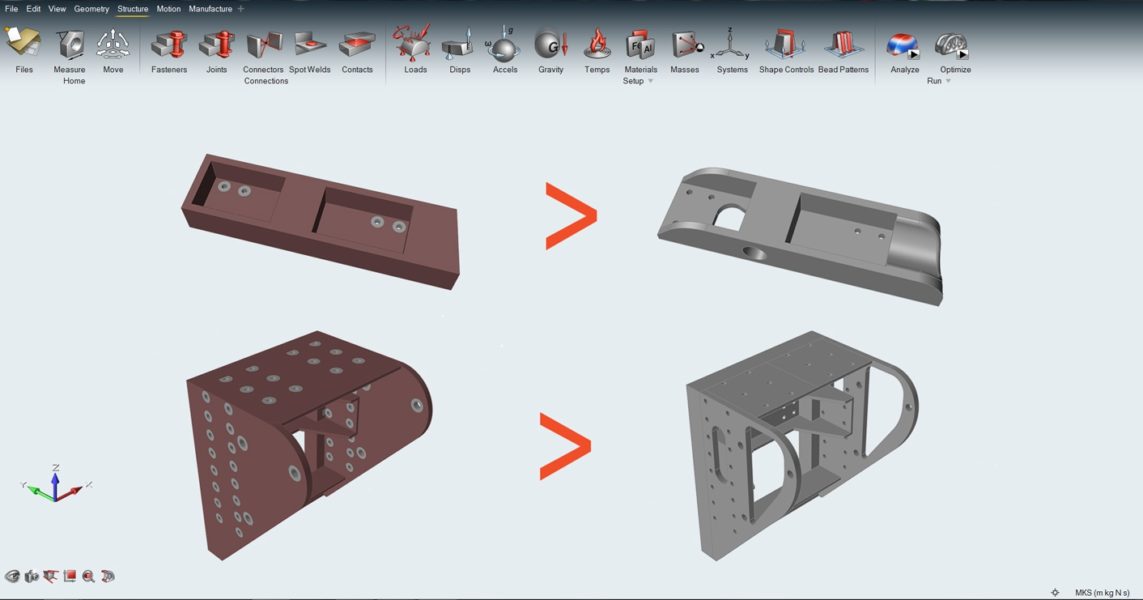
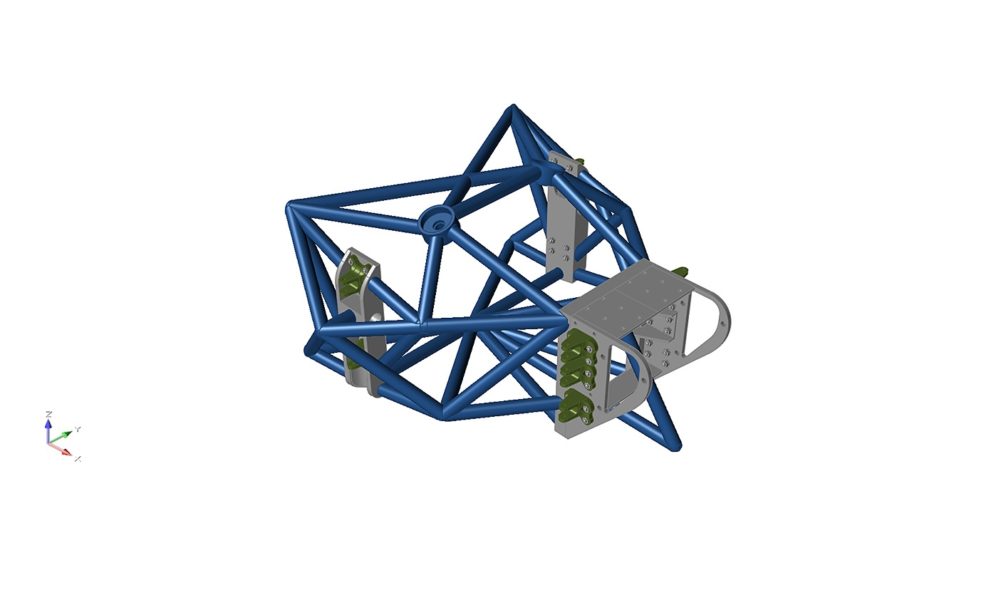
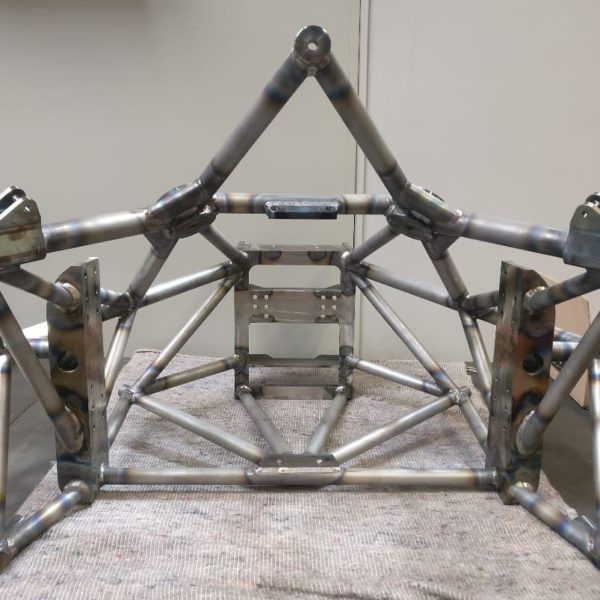
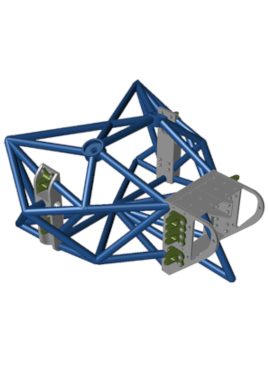